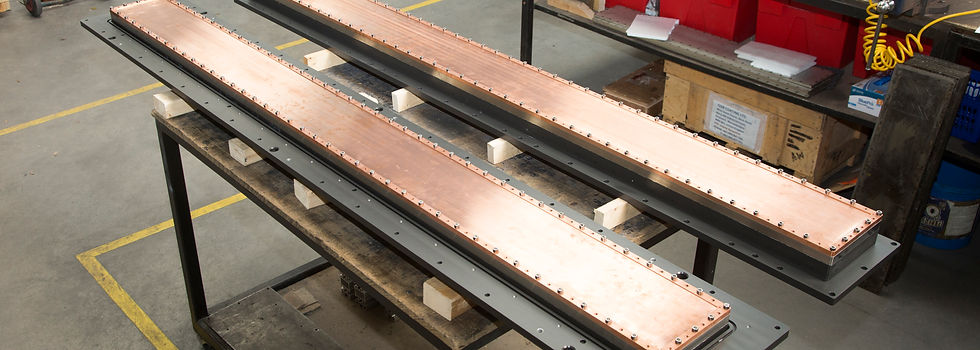
Magnetron Sputtering
Creation of Vacuum conditions
It takes typically 30 minutes of pumping to achieve a vacuum sufficient to begin the coating process – a pressure of less than one ten millionth of an atmosphere. From this point a closely controlled flow of argon, an inert process gas, is introduced, with the pumps still running. This raises the pressure in the system to the levels needed to operate the magnetrons, although it is still only a few ten thousandths of an atmosphere. The combination of pumping down to the high vacuum region and the continual throughput of process gas ensures that coating conditions are both clean and reproducible.
Magnetron sputtering is used at Teer Coatings Ltd to produce some of the highest quality coatings currently available from any technique. These coatings have excellent adhesion to the workpiece and a range of properties tailored to todays demanding engineering applications. Magnetron sputtering is a powerful and flexible technique which can be used to coat virtually any workpiece with a wide range of materials – any solid metal or alloy and a variety of compounds.
To magnetron sputter coat a component it is first precleaned, then jigged and placed inside the coating system. This is a stainless steel chamber equipped with the pumps necessary to produce a high quality vacuum, sample support and rotation equipment and the sources of coating material known as magnetrons.
Application of Magnetrons
A magnetron consists of a plate of the material of which the coating is to be made (called the target) with magnets arranged behind it which create a magnetic trap for charged particles, such as argon ions, in front of the target. When the magnetron drive power supplies are turned on, they put the target at a negative voltage of typically -300V or more, which attracts argon ions to the target surface at speed. When they hit it, two important processes take place:
• Atoms are knocked out of the target surface by the ions – this is sputtering. These sputtered atoms are not charged negatively or positively, so they go straight out of the magnetic trap. It is these atoms which hit the workpieces to form the coating.
• The surface also releases electrons, which are negatively charged sub-atomic particles. These are held in the magnetic trap, where their energy is used to produce more argon ions. This means that the ions which are attracted to the surface are replenished all the time, so that the magnetron can operate continually.
Sputtering also leads to the heating of the target, so the magnetron incorporates channels for water cooling during operation.
Ion cleaning
After pumping down, the workpieces are ion cleaned. During this part of the process the magnetrons are run at a low power, which ionises (electrically charges) atoms of the argon process gas, but sputters very little coating material. When the workpieces are biased to -500V or more they attract the argon ions, which bombard the surface with high energies, removing microscopic surface contamination at the molecular level. When the ion clean is complete the bias voltage on the workpieces is reduced and the power to the magnetrons is increased for the deposition of the coating.
Magnetron Plasma
When a magnetron is in operation (viewed through a window in the chamber wall), the space inside the chamber glows, with particularly bright areas in the magnetic traps at the front of each magnetron. This is because of the way the electrons interact with the argon gas, causing it to become excited, then decay back to its original state, giving off its extra energy as light. This glowing mass of charged particles is known as a plasma.
The exact details of the magnetic trap, and the links between the magnetic traps of adjacent magnetrons have to be carefully designed. Adjusting the strength and size of the magnets can effect not only how efficiently the sputtering process takes place, but also how much plasma surrounds the items being coated.


Closed Field Unbalanced Magnetron Sputter Ion Plating
The Closed Field Unbalanced Magnetron Sputter Ion Plating system, developed by Teer Coatings Ltd, produces optimised deposition conditions allowing deposition of dense, hard coatings with excellent adhesion. The CFUBMSIP arrangement is covered by patents granted to Teer Coatings Ltd.
• UK Patent No 2 258 343,
• USA Patent No 5 556 519,
• European Patent No 0 521 045
Development Of The CFUBMSIP System
Development of the CFUBMSIP system at Teer Coatings began in 1986, when a long term development programme, intended to increase the ion current density in magnetron sputter ion plating, was started. This work led to the development of the closed field system.
The major stage in the development of the system was the idea of using unbalanced magnetrons in an arrangement whereby neighbouring magnetrons are of opposite magnetic polarity. Using this arrangement, the deposition zone in which the substrates are located is surrounded by linking magnetic field lines. This traps the plasma region, prevents losses of ionising electrons and results in significant plasma enhancement.
The use and design of the closed field unbalanced system is covered by patents granted to Teer Coatings Ltd. The patented closed field system covers any magnetron deposition system containing more than one magnetron where the linking of magnetic field lines from neighbouring magnetrons causes plasma enhancement. This includes twin magnetron systems with facing magnetrons of opposing magnetic polarity and four magnetron systems where the arrangement of the polarity of the magnetrons is closed to enhance the plasma.

Closed Field Unbalanced Magnetron Sputter Ion Plating

ION Current Density
Figure 1 shows ion current against substrate bias voltage for different system configurations. The increase in ion current density obtained by using the closed field unbalanced system can be clearly seen.
Coating Structure
From the graph of ion current against bias voltage it can be seen that the maximum ion current is achieved at a bias voltage of around 50V. Therefore deposition can be carried out using a high density of low energy bombarding ions. This results in deposition of very dense, non columnar coating structures with low internal stresses. The use of a low bias voltage during deposition also allows deposition of coatings with dense structures at low temperature.
Coating Adhesion
Figure 2 shows ion current against bias voltage for two different levels of current applied to the magnetrons. Here it can be seen that as the current to the magnetrons is increased there is a corresponding increase in ion bombardment, hence the ratio of ions to neutrals within the system is kept approximately constant. This ensures that the quality of the coatings produced by the system is independent of the deposition rate.
In the CFUBMSIP system ion cleaning prior to deposition is carried out with the magnetrons switched on at low power. The use of magnetrons at this stage allows a plasma to strike to the substrates at low Argon pressure (around 1×10-3Torr) which is much more effective than a high pressure plasma. Ion cleaning is carried out at point B on the graph with deposition at point A. The ion current at point B is approximately 100 times greater than in a conventional system without the closed field arrangement.
Therefore in the CFUBMSIP system the efficiency of ion cleaning is significantly increased, resulting in coatings with very high levels of adhesion.
Systems Covered By The Patents
Any magnetron sputter deposition system containing more than one magnetron where the linking of magnetic field lines from neighbouring magnetrons causes plasma enhancement is covered by the above patents.
This includes twin magnetron systems with facing magnetrons of opposing magnetic polarity. It includes four magnetron systems where the arrangement of the polarity of the magnetrons is closed to enhance the plasma.
The magnetrons may be round or rectangular. They may be oriented with their long axis vertical or horizontal. If linking magnetic field lines enhance the plasma then the above patents are infringed.

Coating Structure